|
MECHANICS - THEORY
|
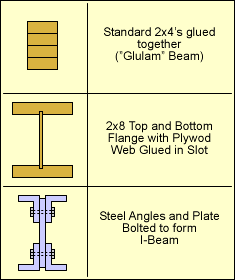
Typical Built-up Beams
|
|
Built-up Members
|
|
This section does not introduce any new equations, but instead deals with how
to use the shear stress equation in designing beams made from various smaller
structural members. By using smaller members, beams can be customized for strength
and sometimes for visual appeal.
Two common wood build-up members is stacked lumber, such as 2x4's. Wood can
be easily glued and modern adhesives are extremely strong (stronger than wood
in most cases).
Structural steel members are usual bolted or welded together. This can be labor
intensive and thus not as common as built-up wood beams.
|
|
|
|
|
|
Built-up Beams Using Adhesives
|
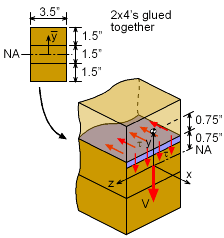
Shear Stress at Adhesive Joint of Glulam Beam. |
|
Since adhesive is applied evenly (hopefully) over the surface, the shear stress
only needs to be less than the allowable shear stress of the adhesive. For example,
if three 2x4's are glued together to form a new built-up beam (commonly referred
to as a "Glulam" beam, short for glued laminated beam), then the shear
stress at the joints should be determined.
The shear stress can be calculated for either joint (will be the same due to
symmetry) using the
shear stress equation presented previously. Assuming V =
10 kip, the shear stress in the adhesive will be
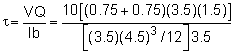
= 10 (7.875) / [26.58 (3.5)]
= 0.8465 ksi
|
|
|
|
|
|
Built-up Beams Using Bolts, Nails, Screws, Rivets, etc.
|
|
|
Unlike adhesive joints, bolts, nails, screws, and rivets (attachment devices)
are not continuous. Thus, the shear stress needs to be converted to a single
load over a given area. Then that load needs to be applied to the attachment
device.
This can be confusing since spacing and location of a given attachment device
may not be known. In fact, the design of built-up beams require the
designer to specify the spacing and location of the attachment devices.
|
|
|
|
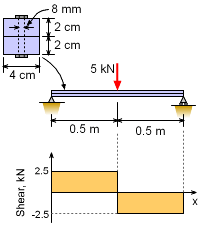
Shear Load in an Example of
a Bolted Built-up Beam |
|
The best way to understand the design of built-up members using attachment devices
is to examine a typical example. Assume a simple support beam is constructed
from two simple steel bars, each 4 cm by 2 cm as shown in the diagram. The two
bars are bolted together with 8 mm diameter steel bolts. There
is a simple center load of 5 kN. Assume the steel can withstand 125 MPa shear
stress (both the bolts and bars). What should be the space between the bolts
along the length of the beam?
First, construct a shear diagram to find the maximum shear load. In this case,
the shear load magnitude is constant at 2.5 kN. Next, determine the actual shear
stress at the joint using the basic shear stress equations,

where I and Q are
I = 0.04 (0.04)3 / 12 = 2.133 × 10-7 m4
Q = (0.01) (0.04) (0.02) = 8.0 × 10-6 m3
This gives
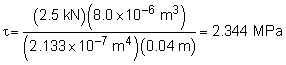
|
|
|
|
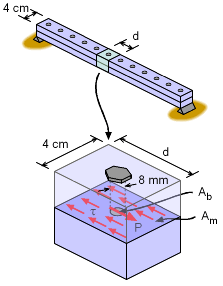
Single Bolt Section |
|
This shear stress, τ, between the members must be carried
by the bolts that are spaced at a distance d. Thus, the shear stress over a distance
d must be carried by one bolt, as shown in the diagram.
The total load, F, from the shear stress over the area Am will be
F = τ Am =
(2.344 MPa) (0.04 m) d = (93.76 d) kN
This load must be carried by the bolt. The allowable shear stress in the bolt, τa
is only 125 MPa. The total bolt load will be
P = τa Ab
= (125 MPa) [π(0.004 m)2] = 6.283 kN
Since P and F must be equal,
F = P
93.76 d = 6.283
d = 0.06701 m = 6.701 cm
In other cases, the bolt size may be unknown, but the spacing given. It is important
to remember that the shear stress must be carried by the bolt (or nail, screw,
rivet, etc.) or an adhesive.
|
|
|
|
|