|
MECHANICS - CASE STUDY
|
|
|
Introduction
|
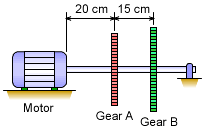
Motor Driving Two Gears
|
|
It has been determined that a mechanical drive system needs to generate 900
N-m torque (clockwise) to turn two gears. Gears A and B have resisting moments
of 500 N-m and 400 N-m respectively (counter-clockwise which is the opposite
direction to the motor moment). The shaft needs to be sized to insure the safe
operation of the system.
What is known:
- The drive shaft is straight and continuous from the motor to the right support.
- The shaft material is an aluminum alloy with E = 69 GPa and ν =
0.33.
- The maximum shear stress of the shaft is 275 MPa.
- A factor of safety of 2.0 is required.
- The rpm of the motor is not known.
|
|
|
|
|
|
Question
|
|
|
Considering the factor of safety, what is the minimum radius so that the shear
stress does not exceed the given stress limit? What is the total
shaft rotation from one end to the other?
|
|
|
|
|
|
Approach
|
|
|
- The motor torque must equal the moment loads applied to the shaft from the
gears.
- The shaft internal moment needs to be determined (may not equal the gear
loads).
- To determine the required radius, use the torsional shear stress
equation,

- After the radius is found, use the angle of twist equation to find
the rotation angle,
|
|
|
|
|