MECHANICS - THEORY
|
|
|
Introduction
|
The internal structure of racing cars
are complex and require detailed
knowledge of mechanics.
|
|
Mechanics of Materials presents topics
that build on the concepts learned in your Statics course. In general,
this course introduces stress and strain (both normal and shear) for basic
structural members (beams, shafts, columns and axial rods), deflection
of beams, column buckling and material failure. Similar to all engineering
courses, there are also many sub-topics.
This course is critical to structural engineers, product reliability
engineers, and equipment design engineers. Without a good knowledge of
stress and strain, and how they can be calculated, no structure can be
well designed and premature failures can and probably will occur.
|
|
|
|
|
|
Static Equilibrium
|
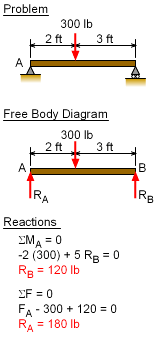 |
|
Mechanics of Materials starts with the basic static equilibrium equations,
Each object in any static structure must be in both force and moment
equilibrium. These equations are used in almost every problem in mechanics
to calculate needed information, such as support reactions,
internal forces, equivalent loads and shear.
Another tool used extensively in mechanics is the Free Body Diagram
(FBD). These diagrams isolate a single member or structure with all boundary
conditions
converted to forces and moments. A FBD helps to identify all loads, forces
and moments (both known and unknown) on a object which can then be used
to solve for unknowns. |
|
|
|
|
|
Problem Solving
|
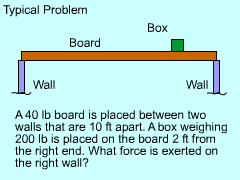
Steps in Solving Problems |
|
In engineering, following a set procedure in solving
problems saves time and decreases the number of errors. Generally, the
following five
steps will help solve problems in mechanics.
- Read and understand the question(s).
a) Identify all given data.
b) Identify exactly what is being asked.
- Make sketches and draw free-body diagrams.
- Set up the problem and apply all relevant
equations.
- Perform the calculations.
- Check and review the answer.
|
|
|
|
|
|
Units
|
Basic Conversion Ratios |
|
1 ft |
= |
0.3048 m |
|
|
1 slug |
= |
14.59 kg |
|
|
1 lb |
= |
4.448 N |
|
|
1 psi |
= |
6.895 kPa |
|
|
|
Whether we like it or not, engineers must be able to work in both US
and SI (metric) units. Conversion ratios relate one set of units to another
set and are commonly used to quickly convert between units. Some basic
ratios are shown at the left. The
Units Appendix
has a large selection of conversion ratios for both SI and US units. |
|
|
|
|
|
Normal Stress
|
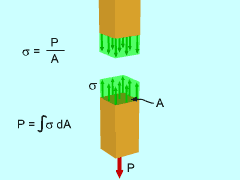
Normal Stress |
|
The most common type of stress in mechanics is a normal stress. A stress is defined as the load divided by the area. For a normal stress, it is all loads perpendicular to the surface. (non-perpendicular loads are addressed in later sections). This relationship can be summarized as
Another way to express the same concept is to define the total perpendicular
load P as

where A is the area of the surface. The symbol σ is used for normal
stress. Later, other symbol, such as τ, are used for other types of
stress
|
|
|
|
|
|
Stress on an Inclined Plane
|
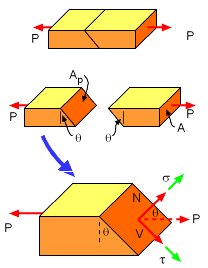
Stress on an Inclined Plane
|
|
In many cases, the stress needs to be determined on a plane that is
not perpendicular to the load direction. This can obtained by using trigonometry
relations, but remember, both the area and load needs to be rotated to
the inclined plane.
N = P cosθ
V = P sinθ
Ap = A/cosθ
Using the definition of normal stress, the stress perpendicular to the inclined
plane is
The stress parallel to the plane (referred to as shear stress) is
|
|
|
|
|
|
Saint-Venant Principle
|
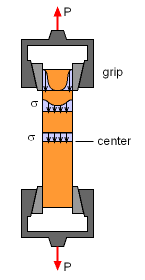
Stress Distribution in a Tensile Test
|
|
The Saint-Venant Principle simply states that localized
stress concentrations disappear a short distance from the concentration
(after Barre de Saint-Venant,
1864). This means that the stress is uniform in a uniaxial loaded bar
away from the ends.
Generally, stress concentrations dissipate quickly. This is illustrated
at the left for a square bar that is pulled using friction grips at both
ends. The grips introduce the tensile load on the surface of the bar, but
quickly, the stress is evenly distributed over the bar. The relationship,
σ = P/A, is only valid away from boundary conditions
that introduce stress concentrations.
|
|
|
|
Factor of Safety
|
|
|
In all design situations, a factor of safety needs to be considered
to help insure the structure does not fail due to unforeseen conditions
such as excessive loading, errors,
and poor craftsmanship. Of course, including a factor of safety does
not
guarantee that the structure will not fail, but it does decrease the possibility
of failure.
Basically, a "factor of safety" (FS) is a multiplication constant that
is applied to the calculated load to give a higher load.
In all cases, the FS is greater than 1. In most cases, the factor of
safety will be 2 or 3. While a high factor of safety sounds good, the penalty
will be an increase in weight. Another way
to consider the FS of a structure is
where the failure stress is the stress level when the material will
fail. Failure or ultimate stress levels for various materials can be
found in handbooks (see
Materials Properties appendix). The allowable stress is the stress
found in the design calculations for the actual applied load.
In addition to FS, some design codes talk about a "margin of safety"
(MS). This is simply a FS less 1, or
MS = FS - 1.0
|
|
|
|