|
THERMODYNAMICS - THEORY
|
|
|
Thermodynamic cycles can be divided into two general
categories: power cycles, which produce a net power output, and refrigeration
and heat pump cycles, which consume a net power input. The thermodynamic
power cycles can be categorized as gas cycles and vapor cycles. In gas
cycles, the working fluid remains in the gas phase throughout the entire
cycle. In vapor cycles, the working fluid exits as a vapor during
one part of the cycle and as a liquid during another part of the
cycle.
Internal combustion engines and gas turbines undergo gas power
cycle.
The two major application areas of gas-turbine engines are
aircraft propulsion and electric power generation. This section will introduce
the ideal cycle for gas-turbine engine - Brayton cycle with intercooling,
reheating, and regeneration.
|
|
|
|
|
|
The Brayton Cycle with Regeneration
|
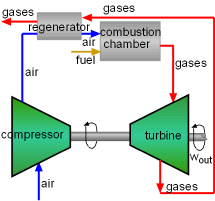
Brayton Cycle with Regeneration
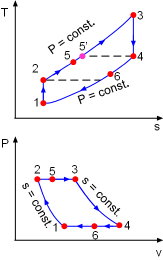
T-s and P-v Diagrams of an Ideal
Brayton Cycle with Regeneration
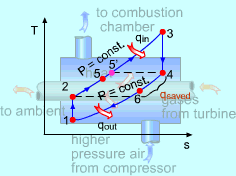
Regenerator Saving Energy Input
|
|
In gas-turbine engines, if the temperature of the exhaust gases from
the turbine is higher than the temperature of the air leaving the compressor,
a counter-flow heat exchanger can be used to increase the temperature
of the air by receiving heat from the exhausted gases, and the counter-flow
heat exchanger is called a regenerator or a recuperator. The thermal
efficiency of the Brayton cycle can be increased since the energy in
the exhaust gases is used as a portion of the heat input and save fuel
requirements for the same net work output.
The T-s and P-v diagrams of an ideal Brayton cycle with regeneration
is shown on the left. Air increases its temperature from T2 to
T5 and the exhausted gases decrease their temperature from
T4 to T6 in the regenerator. In an actual case,
T5 is
less than T4 and T6 is larger than T2.
Heat transferred from the exhausted gases to the air is
qregen, act = h5 - h2
In the ideal situation, air leaves the regenerator
at the same temperature of the inlet exhausted gases (T4),
denoted as T5'. Now the heat transferred from the exhausted
gases to the air becomes
qregen, max = h5' - h2 = h4 -
h2
The ratio of the actual heat transferred from the exhausted gases to
the air to the maximum heat transferred from the exhausted
gases to the air is called effectiveness (ε).
ε = (h5 - h2)/(h4 -
h2)
The effectiveness of most regenerators used in practice is below 0.85.
Under cold-air-assumption, the thermal efficiency of an ideal Brayton cycle with regeneration is
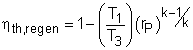
|
|
|
|
|
|
The Brayton Cycle with Intercooling, Reheating, and
Regeneration
|
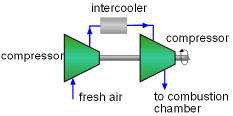
Compressors with Intercooling |
|
The net work output from a gas-turbine is the difference of the work
generated by the turbine and the work consumed by the compressor. The
net work output can be increased by either decreasing the compressor
work or increasing the turbine work, or both. Using multistage compression
with intercooling can decrease the compressor work. This can be shown by the following case.
Assume a compressor needs to compress gas from P1 to P2. Three methods are available.
- Isentopic compression
- Isothermal compression
- Two-stage compression process: Isentopic compressing to a pressure
Px between P1 and
P2, cooling the gas to its original temperature T1,
then isentopic compressing to pressure P2
|
|
|
|
|
|
The compressor works of the three processes are:
Isentropic: 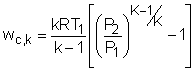
Isothermal: 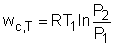
Two-stage: 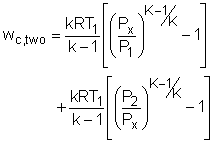
|
|
|
|
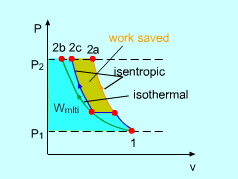
P-v Diagram of Three Processes
to Compress gas from P1 to P2
|
|
The three processes are plotted on a P-v diagram shown on the left.
On a P-v diagram, the area to the left of the
process
curve is the integral of vdP. This is a measure of the steady-flow
compression work. One can observe from this diagram that isentropic compression
requires the maximum work, the isothermal compression requires the
minimum, and two-stage isentropic compression is between. In practice,
it is not possible to compress gas in an isothermal manner. So a technique
called multistage compression with intercooling, where the gas is compressed
in stages and cooled in between each stage to its initial temperature
by passing it through a heat exchanger, is used. This heat exchanger
is
called an intercooler. The two-stage compression illustrated above
is a simple case of multistage compression. Its compressor work varies
with Px.
When Px satisfied the following condition, the compressor
work achieves its minimum.
|
|
|
|
|
|
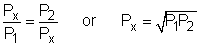
Likewise, the work output from a turbine can be increased by expanding
the gas in stages and reheating it in between. This technique is called
multistage expansion with reheating. Combustion in gas turbines typically
occurs at four times the amount of air needed for complete combustion.
Therefore, reheating can be accomplished by simply spraying additional
fuel into the exhaust gases between two expansion states. For two-stage
expansion, similar with two-stage compression, the turbine work output
reaches its maximum when equal pressure ratios are maintained across
each stage.
When intercooling and reheating are used, the working fluid leaves the
turbine at a higher temperature and the compressor at a lower temperature.
This makes regeneration more attractive. |
|