THERMODYNAMICS - THEORY
|
|
|
Thermodynamic cycles can be divided into two general
categories: power cycles, which produce a net power output, and refrigeration
and heat pump cycles, which consume a net power input. The thermodynamic
power cycles can be categorized as gas cycles and vapor cycles. In gas
cycles, the working fluid remains in the gas phase throughout the entire
cycle. In vapor cycles, the working fluid exits as a vapor during
one part of the cycle and as a liquid during another part of the cycle.
Internal combustion engines and gas turbines undergo gas power
cycle.
The two major application areas of gas-turbine engines are aircraft
propulsion and electric power generation. This section introduces
the ideal cycle for gas-turbine engine
- Brayton cycle and jet-propulsion cycle for aircraft propulsion.
|
|
|
|
|
|
Brayton cycle - the Ideal Cycle for Gas-turbine
Engine
|
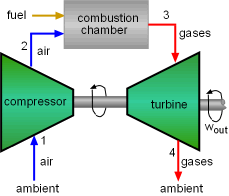
An Open Gas-Turbine Cycle |
|
Gas-turbines usually operate on an open cycle, shown on the left.
- A
compressor takes in fresh ambient air (state 1), compresses it to a higher temperature and pressure (state 2).
- Fuel and the higher pressure air from compressor are sent to a
combustion chamber, where fuel is burned at constant pressure. The
resulting high temperature gases are sent to a turbine (state 3).
- The high temperature gases expand to the ambient pressure (state
4) in the
turbine and produce power.
- The exhaust gases leave the turbine.
Part of the work generated by the turbine is sent to drive the compressor.
The fraction of the turbine work used to drive the compressor is called the back work ratio.
|
|
|
|
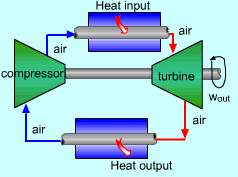
The Ideal Brayton Cycle |
|
Since fresh air enters the compressor at the beginning and exhaust
are thrown out at the end, this cycle is an open cycle.
By utilizing the air-standard assumptions, replacing the combustion
process by a constant pressure heat addition process, and replacing
the exhaust discharging process by a constant pressure heat rejection process, the open cycle
described above can be modeled as a closed cycle, called ideal Brayton
cycle. The ideal Brayton cycle is made up of four internally reversible
processes.
- 1-2 Isentropic compression (in a compressor)
- 2-3 Constant pressure heat addition
- 3-4 Isentropic expansion (in a turbine)
- 4-1 Constant pressure heat rejection
|
|
|
|
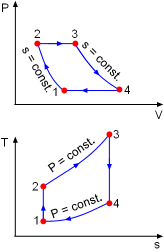
P-v and T-s Diagrams of Ideal Brayton Cycle |
|
The P-v and T-s diagrams of an ideal Brayton cycle are
shown on the left. In an ideal Brayton cycle, heat is added to the cycle
at a constant pressure process (process 2-3).
qin = h3 - h2 = cP(T3 - T2)
Heat is rejected at a constant pressure process (process 4 -1).
qout = h4 - h1 = cP(T4 - T1)
Then the thermal efficiency of the ideal Brayton cycle under the cold air-standard assumption is given as
|
|
|
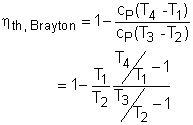
Process 1-2 and process 3-4 are isentropic processes, thus,
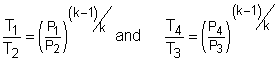
Since P2 = P3 and P4 = P1,
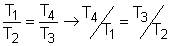
Considering all the relations above, the thermal efficiency becomes,
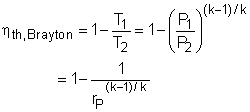
where rP = P2/P1 is the pressure ratio and k is the specific heat ratio. In most designs,
the pressure ratio of gas turbines range from about 11 to 16.
|
|
|
|
|
|
Actual Gas-turbine Cycle
|
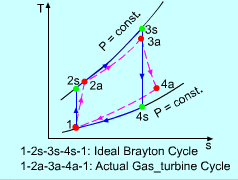
T-s Diagram of Actual Gas-turbine Cycle |
|
The actual gas-turbine cycle is different from the ideal Brayton cycle
since there are irreversibilities. Hence, in an actual
gas-turbine cycle, the compressor consumes more work and the turbine
produces less work than that of the ideal Brayton cycle.
The irreversibilities in an actual compressor and an actual turbine can
be considered by using the adiabatic efficiencies of the compressor and turbine. They
are:
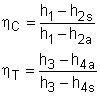
Another difference between the actual Brayton cycle and the ideal cycle
is that there are pressure drops in the heat addition and heat rejection processes. |
|
|
|
|
|
Gas-
Turbines for Aircraft Propulsion
|
|
|
Gas-turbines are widely used to power aircraft. Aircraft gas turbines
operate on an open cycle called a jet-propulsion cycle. Jet-propulsion
cycle differs from the Brayton cycle in the gas expansion process.
In Brayton cycle, gases are expanded to ambient conditions, but in jet-propulsion
cycle, the gases are expanded to a pressure such that the power produced
is only enough to drive the compressor and the auxiliary equipment. Therefore,
the net work output of a jet-propulsion cycle is zero. The high pressure
gases exit from the turbine are sent to a nozzle. They are accelerated in the nozzle to provide the thrust to propel the aircraft. Also, aircraft gas
turbines operate at higher pressure ratios (between 10 and 25). To get
a high pressure before the compression process, the fluid passes through a
diffuser first. |
|
|
|
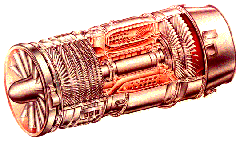
A
Turbojet Engine |
|
Aircraft are propelled by accelerating a fluid in the opposite direction
to motion. Propeller-driven engine accomplishes this by slightly accelerating
a large mass of fluid, jet or turbojet accomplishes this by greatly accelerating
a small mass of fluid, and turboprop engine uses both.
In a turbojet engine, the cycle proceeds as follows,
- In the diffuser, air increases its pressure slightly.
- Air is compressed to a higher pressure in the compressor.
- Air mixed with the fuel in the combustion chamber and the mixture
is burned at constant pressure.
- The high pressure, high temperature gases exit from the combustion
chamber and expand in the turbine to generate enough power to drive
the compressor and the auxiliary equipment.
- The gases expand in a nozzle to the ambient pressure and leave the
engine at high velocity.
|
|
|
|
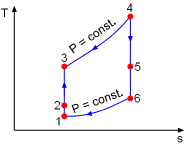
T-s Diagram of an Ideal Turbojet Cycle
|
|
In an ideal jet-propulsion cycle, the power generated in the turbine
equals the power consumed in the compressor. And the processes in the
diffuser, compressor, turbine and nozzle are assumed to be isentropic. The T-s diagram is shown on the left.
The thrust force developed in a turbine engine can be determined from
Newton's second law. According to the Newton's second law, the thrust
produced by the jet engine is equal to the rate of change of the momentum
of the fluid flowing through the engine. When the inlet and exit pressures
of the engine are identical, the thrust force is

|
|
|
|
|
|
where
vexit = velocity of gases exhausted from the
nozzle,
relative to
the aircraft.
vinlet = inlet air velocity, relative to the aircraft.
Propulsive power ( )
is the propulsive force times the distance this force acts on the aircraft
per unit time, which is the aircraft velocity.
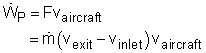
The efficiency of a turbojet engine is defined through the general definition since the net work output is zero. The desired output
in a turbojet engine is the propulsive power and the required input is the
thermal energy of the fuel released in the combustion process. This efficiency
is called the propulsive efficiency.

The propulsive efficiency measures how much energy released in the combustion
process is converted to propulsive energy. |
|
|
|