|
When fluid flows over an immersed body,
forces are exerted on that body. The resultant force parallel to the fluid motion is referred to
as the drag. Determining drag is important in many engineering applications,
such as the design of automobiles, airplanes, submarines and buildings.
Drag (D) consists of both friction and pressure drag, and it is often
expressed in terms of a drag coefficient (CD) as
where ρ is the fluid density; A is the characteristic
area and V is the upstream velocity. The characteristic area can be choosen
as: (a) the projected frontal area (often used for flow over automobiles
and submarines), (b) the planform area (often used for flow over wings and
hydrofoils), and (c) the wetted area (often used for flow over ships
and barges). Hence, it is important to know which characteristic area
was used when determining the drag coefficient.
Generally, the drag coefficient is determined through experiments, and
it depends on parameters, such as the body shape,
Reynolds number and surface roughness. The value of the drag coefficient
for different body shapes subject to different flow conditions are
available in the literature.
Some of the drag coefficients for flow over two-dimensional and three-dimensional
bodies are summarized in the following tables.
|
Drag Coefficient for
Two-Dimensional Body
(**Note: b is the length into the page) |
|
Drag Coefficient for
Three-Dimensional
Body
Shape |
Area,
A |
Reynolds
Number
Re |
Drag Coefficient
CD |
Cube
 |
D2 |
> 104 |
1.05 |
Hemisphere  |
πD2/4 |
> 104 |
1.17 |
 |
0.42 |
Cylinder
 |
πD2/4 |
> 104 |
L/D =0.5 => 1.10
L/D =1.0 => 0.93
L/D =2.0 => 0.83
L/D =4.0 => 0.85 |
Cone
|
πD2/4 |
> 104 |
θ =10o => 0.30
θ =30o => 0.55
θ =60o => 0.80
θ =90o => 1.15 |
|
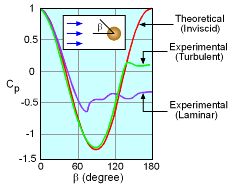
Pressure Distribution for
Flow around a Sphere
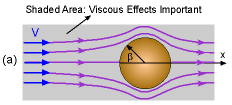
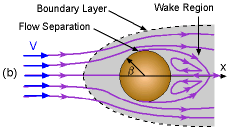
Characteristics of Flow over Sphere Subject to Different Reynolds Numbers:
(a) Re << 1,
(b) 1×103 < Re < 2×105
(c) Re > 2×105
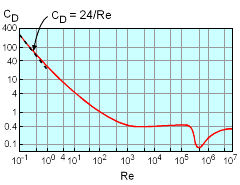
Drag Coefficient as a Function of the Reynolds Number for a Smooth Sphere
|
|
Consider flow over a sphere for illustration. Unlike
flow over a flat plate,
the pressure field of flow over a sphere is not uniform. This can be
seen from the pressure distribution (i.e., )
around a sphere given in the figure.
At low Reynolds numbers (i.e., Re << 1), the viscous effects are important in a large
area (shaded area). There is no flow separation, and the fluid is stuck
to the sphere. The drag coefficient as a function of the Reynolds number is shown in the figure. At very small Reynolds numbers, Stokes
has shown that the drag coefficient is a linear function of the Reynolds number, as given by
CD = 24/Re
At moderate Reynolds number (103 < Re < 2×105),
a boundary layer is developed near the sphere. Viscous effects
are important inside the region of this boundary layer. Due to the increase of the pressure drag, the fluid can no longer stick to the sphere, and it is separated at an angle (β) of about 80o.
A broad wake region is formed downstreams. Note that the drag
coefficient decreases with the Reynolds number, and it becomes almost a constant (CD =
0.4) for a Reynolds number between 103 and 2×105.
As the Reynolds number increases (Re > 2×105),
the boundary layer becomes thinner in the front of the sphere and begins
its transition to turbulent. The flow separation is
delayed until an angle of about 120o, and
the fluid forms a relatively narrow wake
region in which the flow is highly unsteady and turbulent. For turbulent
boundary layer flow, the drag coefficient is decreased further (e.g.,
CD = 0.06 for Re = 4×105).
Hence, a turbulent boundary layer develops as
fluid flows past an object will reduce the drag force.
For example, the dimples of a golf ball (i.e., the surface roughness
of the object) are used to create turbulent boundary
layer flow, and hence reduce the drag force.
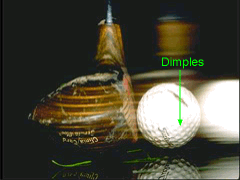
Dimpled
Golf Ball: Reduce Drag
|
For Android mobile devices, "Flow HPC", can be downloaded at Google Play.
For iOS (Apple) mobile devices, "Flow HPC", can be downloaded at iTunes.
|
|
Determining drag for unique shapes can be relatively difficult even for numerical methods. Basically, the full nonlinear Navier-Stokes equations must be solved. For low Reynolds number it is manageable using finite element method. A simple demonstration simulation is given below. It currently only works for Re < 50. |