MECHANICS - THEORY
|
|
|
Introduction
|
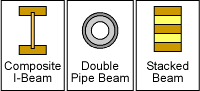
Various Examples of Two-Material Composite Beams |
|
Composite beams are constructed from more than one material to increase stiffness
or strength (or to reduce cost). Common composite-type beams include I-beams
where the web is plywood and the flanges are solid wood members (sometimes referred
to as "engineered I-beams"). Pipe beams sometimes have an outer liner
made from another type of material.
In this section, two-material composite beams will be examined. Of course, two materials
can be arranged in multi-sections but only two different type of materials will
be used. Beams with three or more materials are possible, but are rare and increase
the complexity of the equations. |
|
|
|
|
|
Two-material Composite Beams
- Axial Load
|
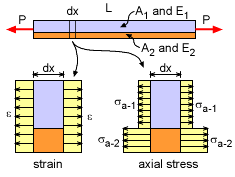
Strain and Stress in Two-material Composite Beam undergoing
Axial Loading |
|
The simplest loading in a composite beam is
axial loading. The strain is continuous across the beam
cross section but the stress is discontinuous as shown in the diagram at the
left. When axially loaded, the normal strains are equal since the two materials
are rigidly attached. From Hooke's law, this gives
ε1 = ε = σ1/E1
ε2 = ε = σ2/E2
Eliminating ε gives,
σ1/E1 = σ2/E2
The total load P must equal the stresses times their respective areas, or
P = A1σ1 +
A2σ2
Combining the previous two equations gives
|
|
|
|
|
|
Two-material Composite Beams
- Moment Load
|
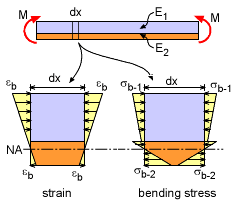
Strain and Stress in Two-material Composite Beam undergoing
Moment Loading |
|
Similar to axially loaded two-material beams, when a beam is subjected to a
moment, the strain is still continuous, but the stress is discontinuous. Where
the stress and strain in axial loading is constant, the bending strain and stress
is a linear function through the thickness for each material section as shown
at the left.
The bending stress equations require the location of the neutral axis. For non-composite
beams, the neutral axis (NA) is the centroid of the cross section. This is not
the case for composite beams and is one of the main difficulties in solving for
the bending stress. Thus, the first step in calculating bending stress is locating
the NA. Then the
bending stress equation, My/I, can be used to find the
stress in each material. There will be a separate equation for the bending stress
in each material section. |
|
|
|
|
|
Neutral Axis (NA) Location
|
|
|
As with non-composite beams, the neutral axis (NA) is the location where the
bending stress is zero. The location of the NA depends on the relative stiffness
and size of each of the material sections.
Generally, the NA location is determined relative to the bottom surface of the
beam. However, this is not mandatory, and the location can be relative to any location.
If the bottom is used, then the NA axis is a distance "h" from the
bottom as shown in the diagram at the left. |
|
|
|
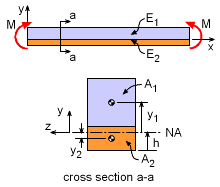
Neutral Axis Location for
Composite Beam |
|
The distance h can be determined by recalling that the stresses through
the cross section must be in equilibrium. Summing forces in the x-direction gives,
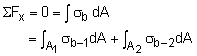
Recall, the bending stress in any beam is related to the radius
of curvature, ρ, as σ =
-Ey/ρ,
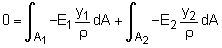
Since the curvature is the same at all locations of a given cross section, this equation simplifies to

The two integrals are the first moment of each material area which is commonly
noted as simply Q, giving
Generally, Q is not solved using the integral form since the centroid of each
material area will be known (or found in the
Sections appendix). Thus the equation
can also be written as
|
0 = E1 (y1 A1) + E2 (y2 A2) |
|
where y1 and y2 are the distance from the NA to the centroid
of the material area. Notice, "h" is not in this equation, but both y1 and
y2 depend
on h. Thus, the only unknown will be h and can be determined. Note, y will be negative if the centroid of the material area is below the NA. |
|
|
|
|
|
Bending Stresses
|
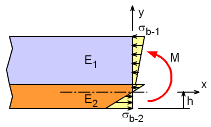
Neutral Axis Location for
Composite Beam |
|
The bending stress in a composite beam can be found by using the moment equilibrium
equation at any internal location. Summing the moments give,
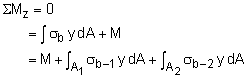
Using the relationship between the bending stress and the radius
of curvature, σ =
-Ey/ρ, gives,

Notice that the integral is the second moment of the area which is also the
area moment of inertia, I. This simplifies to
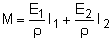
Rearranging gives
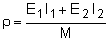
The bending stress in each material section is related to the beam curvature
as

Substituting the curvature into the above equations gives the final bending
stress for each material section.
Each equation is only valid for its material area. Also, these two equations
are for two-material composite beams only. |
|
|
|
|
|
Alternative Method - Equivalent Area
|
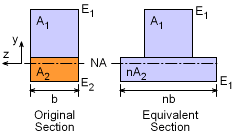
Equivalent Area Method Cross Section |
|
Another way to analyze composite beams is to use an equivalent area to represent the increased (or decreased) stiffness of the second material. The new equivalent cross section is assumed to be made completely from material 1. The area of material 2 is simply scaled to account for the stiffness difference using the scaling factor, n,
n = E2 / E1
Note, the area scaling must only be done in the horizontal direction. The vertical dimension of either material cannot be changed.
The neutral axis can be found by finding the centroid of the full cross section, as was done with single material beams. Also, the bending stresses can be determined from the basic beam bending equation,
where I is the moment of inertia of the full equivalent cross section, and y is the distance from the neutral axis (down is negative).
While this method simplifies the equations, it is still basically the same calculations. It is important to be make sure the scaling factor, n, is correctly determined and applied to the area of the second material.
|
|
|
|