MECHANICS - CASE STUDY SOLUTION
|
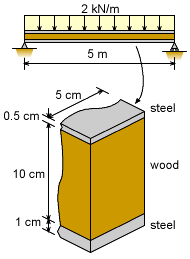
Beam Cross-Section |
|
The ceiling beam is composed of three parts, two steel plates and a wood member.
The plates are rigidly attached to the top and bottom surface of the wood member
as shown in the diagram at the left. The beam must support a continuous load
of 2 kN/m over a simple support span of 5 m.
The beam is a composite beam of only two materials even though there are three
sections. The wood will be treated as one material and the two plates will be
treated as a single material with two areas.
The first issue is to find the actual maximum moment. This is needed for the
composite beam bending stress equations. Next, the neutral axis needs to be determined.
From there, the actual moment of inertia for each material can be found. |
|
|
|
|
|
Maximum Moment
|
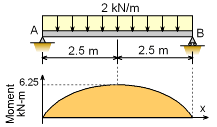
Beam Loading and Moment Diagram
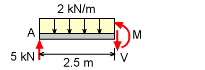
Beam Cut at Center |
|
To determine the maximum bending stress, the maximum bending moment is needed.
This moment is not a function of the cross section and can be determined by the moment diagram. This is a common beam loading and the maximum moment
is at the center.
Cutting the beam at the center and summing the moments gives
ΣM = 0
M - 5 (2.5) + 2 (2.5) (2.5/2) = 0
M = 6,250 N-m |
|
|
|
|
|
Neutral Axis
|
|
|
The location of the neutral axis (NA) is one of the most critical steps when
solving for bending stresses in composite beams. Both the moment of inertia and
the distance to the outside edge of both materials require knowing where the
NA is located. |
|
|
|
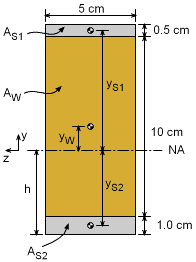
Beam Cross Section |
|
The NA can be determined from the equation
0 = EW QW + ES QS
The steel section consists of two parts, 1 and 2, giving,
0 = EW (yW AW)
+ ES [(yS1 AS1) + (yS2 AS2)]
= 12 (5 + 1 - h) (5) (10) +
200[
(10 + 1 + 0.5 - 0.25 - h) (5) (0.5) +
(-h
+ 0.5) (5) (1) ]
= 3,600 - 600h + 5,625 -
500h + 500 - 1000h
9,725 = 2,100 h
h = 4.631 cm
Now that the distance h is known, the location of all material area centroids
from the NA can be found.
yW = 5 + 1 - 4.631 = 1.369 cm
yS1 = 10 + 1 + 0.5 - 0.25 - 4.631 =
6.619 cm
yS2 = - 4.631 + 0.5 = -4.131 cm |
|
|
|
|
|
Moment of Inertia for Each Material
|
|
|
With the neutral axis (NA) located, the moment of inertia about the NA for each
of the two material areas can be calculated. Using the
basic formula for the moment of inertia of rectangular areas, and the
parallel axis theorem, gives,
IW = h3 b / 12 + yW2 AW
= 103 (5) /
12 + 1.3692 (10) (5)
= 510.4 cm4
IS = IS1 + IS2
= h3 b / 12 + yS12 AS1 +
h3 b / 12 + yS22 AS2
= 0.53 (5) / 12 + 6.6192 (0.5)
(5) +
13 (5)
/ 12 + (-4.131)2 (1) (5) +
= 195.3 cm4 |
|
|
|
|
|
Maximum Bending Stress
|
|
|
The bending stress in each of the material areas can now be determined by using the bending stress equations for a two-material composite beam. There are two equations since each material section has different stress.
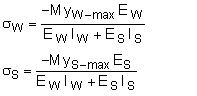 |
|
|
|

Beam Cross Section |
|
The y distance is the maximum distance from the neutral axis for
each material section.
yW-max = (10 + 1 + 0.5) - (0.5 + 4.631) = 6.369 cm
yS-max = (10 + 1 + 0.5) - 4.631 = 6.869 cm
Substituting values into both stress equations give,
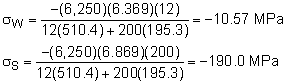
The beam will fail, even though the bending stress in the wood is below the wood failure stress of 50 MPa since the maximum bending stress in the steel is over 150 MPa. If the beam was only wood, it would still fail since the maximum bending stress would be 75 MPa (calculations not shown) which is beyond the failure stress of 50 MPa.
|
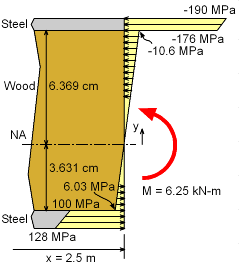
Bending Stress Through Beam
at Center of Beam Span |
|
|
|
Bending Stress Distribution
|
|
To better understand visually how the bending stress varies across the beam, it has been plotted at the left. Notice that the bending stress jumps at the interface between the materials. This is due to the jump in material stiffness (Young's modulus). On the other hand, the strain does not jump and is continuous from the top to the bottom. |
|
|
|