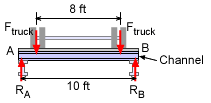
Free Body Diagram of Typical Channel Member
|
|
Like all mechanics problems, a free body diagram of the structure is critical
in solving the problem. In this case, a 19 ton truck is on a 10 ft wide bridge.
The rear wheels are 8 ft apart and carry 80% of the load. The total truck load
(including truck) is 19 tons. Thus, each of the rear wheel sets (one on each
side) will carry 40% of the 19 tons, giving,
Ftruck = 0.4 (19 tons) (2 kip/ton)
= 15.2 kip
The reaction forces are the same as the truck force due to symmetry.
RA = RB = 15.2 kip
|
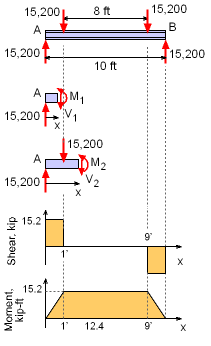
Moment and Shear Diagrams
|
|
A shear and moment diagram of the channel will help identify the maximum shear
load and bending moment. Both of these values are needed to determine the maximum
shear and bending stress.
Due to symmetry, only two cuts are needed to construct the shear and moment
diagrams. The first cut is between RA and the first wheel.
V1 = 15.2 kip
M1 = 15.2 x kip-ft
The second cut is between the left wheel load and the center line of the channel
beam.
V2 = 0.0 kip
M2 = 15.2x - 15.2 (x-1) = 15.2 kip-ft
The moment in the channel beam is constant between the wheels and the shear
is zero. The maximum shear is at either end of the channel. The moment
maximum is between the wheels.
|
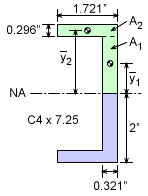
First Moment of the Area, Q,
at the Neutral Axis
|
|
As with any structural member, the shear stress varies across the channel cross
section. It starts at zero at the top and bottom surface and is a maximum at
the center or neutral axis. The shear stress at any point on the section is given
by

To calculate the shear stress
four values are required, V, I, b and Q. The maximum shear load, V, has been
found to be 15.2 kip at either end of the channel. The moment of inertia about
the NA can be found in the appendix
for a C4 x 7.35 channel and is given as 4.59 in4.
The member width, b, at the neutral axis is 0.321 in.
The final term, Q must be calculated using the method of parts. The section
above the cut line (NA) is split into two rectangular parts as shown in the diagram.
This gives,

= (1.704/2)(1.704)(0.321)
+
(2 - 0.296/2)(1.721)(0.296)
= 0.4660 + 0.9434 = 1.4095
in3
Substituting all values in the shear stress equation gives,
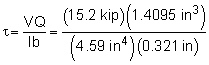
= 14.54 ksi
This is less than the allowable shear stress of 18 ksi.
|
|
|
The bending stress also needs to be checked. Unlike shear stress, the maximum
bending stress occurs at the point furthest from the neutral axis. This is
at the top or bottom surface. Using the bending stress equation gives,
σ = -My/I
= -(15.2 kip-ft)(12 in/ft)(-2
in) / (4.59 in4)
= 79.48 ksi
This is higher than the allowing bending stress of 36 ksi. Thus, the bending
stress will cause failure even though the shear stress is below the allowable
level.
|