MECHANICS - THEORY
|
|
|
Thermal Strain
|
Material |
US
(×10-6/oF) |
SI
(×10-6/oC) |
Steel |
6.5 |
12 |
Aluminum |
13 |
23 |
PVC |
30 |
55 |
Concrete |
5.5 |
10 |
Coefficient of Thermal Expansion, α,
for Common Materials
(Expanded List in Appendix)
|
|
When physical materials are heated, they generally expand due to atomic-level
changes. This expansion is proportional to the change in temperature. In terms
of strain, this relationship is written as
where α is the coefficient of thermal expansion.
This constant is different for all materials and is generally a positive number.
There are a few materials that contract when heated, and then this constant would
be negative.
The coefficient of thermal expansion represents a quantity (i.e. strain) per
degree C or per degree F.
|
|
|
|
|
|
Thermal Expansion
|
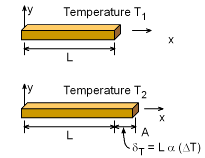
Thermal Expansion where
ΔT = T2 - T1
|
|
The total deflection of a member that undergoes a temperature change, ΔT
= T2 - T1, can also
be written as
The deflection is in the direction of the length L.
For a 3D homogenous object, thermal
expansion will occur in all three directions. The total deflection in any
given direction will be a function of the length, width or depth of the object.
There is no shear strain or shear deflection due to thermal expansion.
|
|
|
|
|
|
Combined Thermal and Mechanical
Strain or
Deflection
|
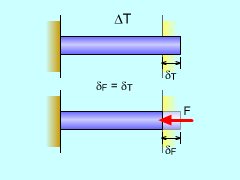
Rod Between Two Fixed Walls -
Example of Stresses induced
by
Thermal Expansion |
|
Generally, thermal expansion is accompanied with mechanical deflection caused
by a physical load. When both force and temperature changes are present, special
care is needed when solving the problem. Both the thermal and mechanical deflections
need to be compatible.
For example, if a simple rod is placed between two fixed walls and heated, the
rod will try to expand. However, the walls will prohibit the normal thermal expansion
and induce a compression force. This force is real and causes the rod to decrease
in length. The final result is the thermal expansion is offset by the mechanical
compression deflection (see diagram and animation at left).
When both mechanical and thermal conditions are present, a compatibility relationship
needs to be introduced to solve the problem. Further discussion of compatibility
conditions can be found in the following section on
Indeterminate
Axial Structures.
|
|
|
|
|
|
Other Material Properties
|
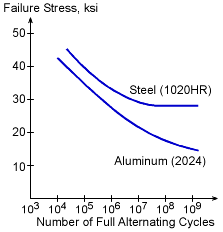
Stress-Cycle (σ-n) Curves
(also called s-n Curves)
|
|
Cyclic Loading (Fatigue)
As structural members experience multiple loading/unloading, their failure stress
level will decrease. For example, car axles or even
aircraft wings will experience millions of loadings over their
service life. For aluminum, the failure stress can reduce by 70% of the original
failure stress level.
To assist designers, charts called s-n curves are
developed through experiments. The charts show the failure stress changes as
the object is subjected to cycles. In some industries, such as aircraft, extensive
testing on full scale models are required to insure the structure will not failure
before a certain number of load cycles.
|
|
|
|
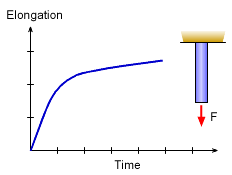
Typical Creep Curve |
|
Viscoelasticity (Creep)
Another interesting property of many materials, especially plastics, is viscoelasticity
or creep. This property models a material's tendency to flow over time when under
stress. The most common effect of this is the deformation of an object over time
when under a very low load. Even glass will creep over time. Plastics tend to
exhibit higher creep characteristics then metals or ceramics.
|
|
|
|